These two series compare and contrast in close details. Both have properties that make manufacturers prioritise the other depending on the goal of the project. Today, we’re going to analyze their properties, applications, and the difference in alloy composition.
Properties of 7075
The 7075 series has smooth production ability and gives the producer the ability to offer custom services. It’s best for applications requiring high stress structures. The alloy has also been repeatedly used in the aircraft structural part production. Here are some of the properties of this alloy.
The alloy has a young modulus reading of 71.7 GPa and tensile strength of 572 MPa. Besides, the elongation at break stands at 11% although this changes depending on the alloy temper. To achieve this, Aluminum metal and Zinc have been used dominantly in composition.
With a density of 2.81 g/cc, the alloy has a melting temperature of 477 degrees Celsius and a Poisson’s ratio of 0.33. Also, the 7075 alloy has a hardness record of 87 HRB according to the Rock well scale.
Going on, the thermal conductivity range of this alloy is between 130 and 150 W/m*K and specific heat capacity of 714.8 J/Kg*K. The resistivity volume stands at 51.5 nOhm*m. In addition to that, the alloy has a yield strength of 140MPa. Again, this figure changes depending on a number of factors.
With the above properties, the alloys is able to get a good rating when considering ductility. Not only that, alloy 7075 has a high strength and great toughness scores. It’s resistance to fatigue is good and it is very high corrosion resistance properties.
The 7075 series
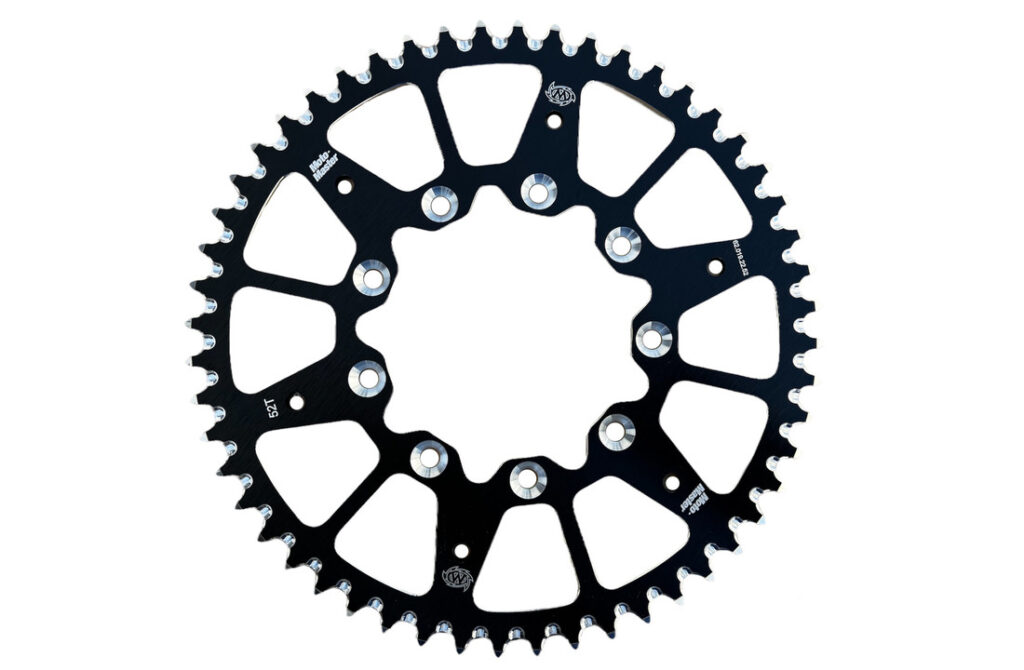
The 7075 alloy has a number of tempers made through ageing process. This adjusts the product’s properties by a margin. The result is usually a more suitable alloy with a better performance ability. Here are some of the most common 7075 tempers you should try.
7075-T6 Temper
This one has a slightly lower tensile strength ranging between 510 and 540 MPa. On the contrary, it has a higher yield strength than normal 7075 alloy at 430-480. This temper is arrived at when the alloy is homogenised at 450 degrees Celsius then quenched. After that, ageing is done at 120 Degrees Celsius for an additional 24 hours. By performing these processes, you make the T6 series which has one of the best yield strengths in the series.
7075-T651
This has a 570MPa and yield strength of 500MPa. The other property is its elongation at break ranging between 3 and 9%. This range depends on the material used in the tempering process. Thicker plates show lower strengths and elongation. The reverse is true. This one shows slightly superior qualities to the plain T6 temper.
7075-T7
This temper has an ultimate strength of 505 MPa and yield strength of 435 MPa. The failure elongation stands at 13%. Overaging is the process that’s used to make this temper. The T7 series also exhibit lesser stress corrosion cracking compared to the T6 series.
7075-RRA
This has higher temperatures and is also achieved through overaging. Time is of essence in the process. During the tempering process, keeping the alloy a little longer in extreme temperatures makes it possible to achieve this temper. Its characteristics and most properties fall in between the T6 and T7.
Applications of 7075 Aluminum Alloy
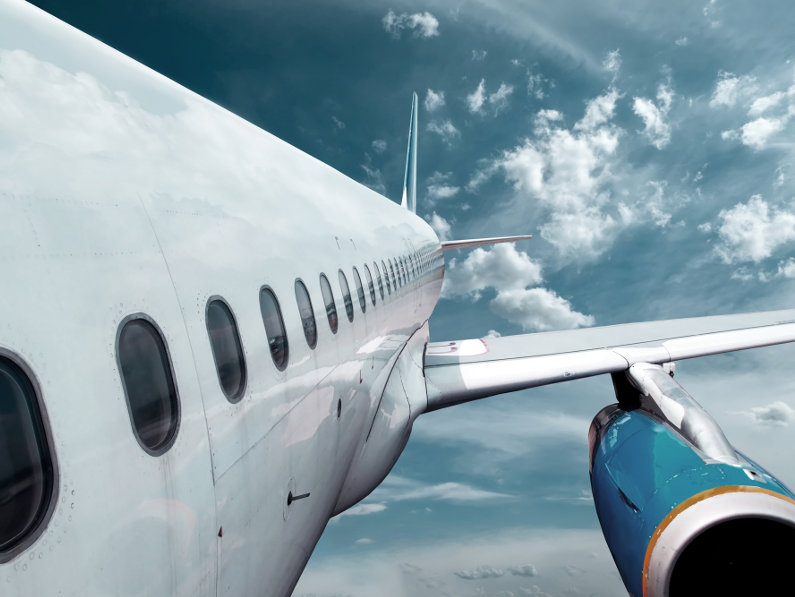
The alloy is applied in a number of industries as listed below:
- Manufacturing
- Equipment
- Aerospace
- Defense
- Military engineering
- Mechanical systems
- Industrial machinery
In all the above industries, the alloy is used to design quality and durable products. Some of the notable products made of this include elbows, tees, crosses, and caps. Those are not all, other products made out of Aluminum 7075 alloy include plugs, connectors and adapters. Other manufacturers also use the alloy to design and produce amazing reducers and bulkhead fittings.
Rock climbers also benefit big time from this alloy. Rock climbing equipment as well as bicycle components have been developed using this alloy. Their light nature and low density makes this alloy the better option. It becomes easier for the hiker or biker to use light climbers and ride lighter bikes respectively.
The 7075T6 extruded aluminum has also been found to be among the best for applications in the aerospace, marine, and transport industries. Therefore, Defense forces benefit greatly from this temper.
Other products made from this alloy include sanitary, air, and hydraulic equipment. In the manufacturing industry, high purity industrial fittings that are also recyclable are made using this alloy. There are many more applications for this alloy.
What makes the 7075 alloy attract such us its properties. Mechanical, physical and all the others combine perfectly to equip this alloy the necessary requirements to make top equipment. Its high strength, thermal properties and an amazing power to be polished makes the alloy stand out.
6061 Properties
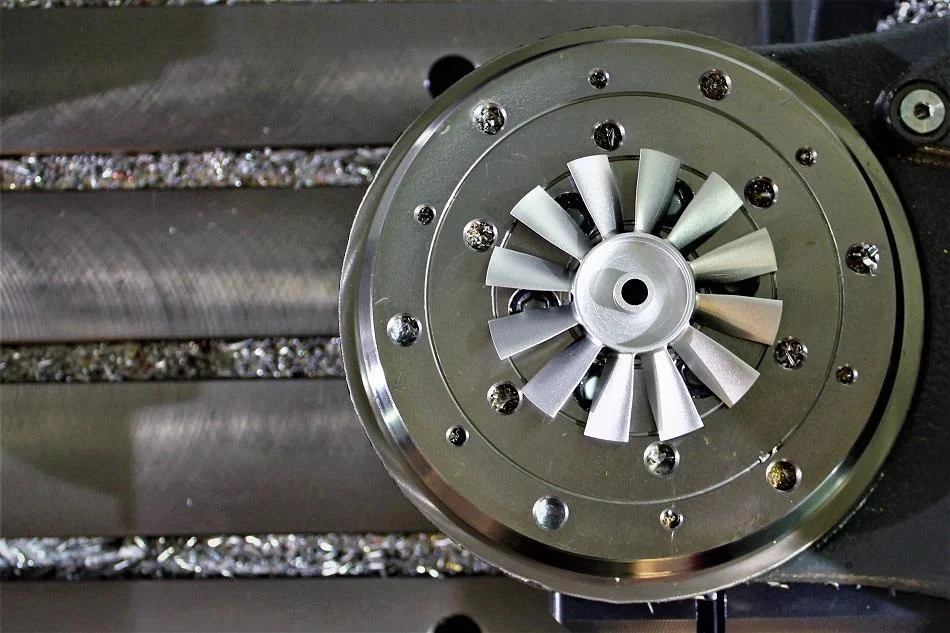
The 6061 series has good machinability and workability when cold. The weldability is also impressive when the alloy is in gas form. It becomes better when in arc state. Both resistance, brazability, and solderability properties of this alloy are impressive. With a density of 2.7 g/cubic centimetres, the alloy melts at 650 degrees Celsius and has a modulus of elasticity at 70 GPa.
Thermal conductivity of alloys also determine much. Its important to note that heat treatment affects the physical properties of an alloy. This alloy is heated treatable and that’s why you can temper it to other series like T4 and T6. The alloy’s thermal conductivity and electrical resistivity stand at 166 W/m.K and 0.04×10^-6 respectively. All these physical properties are somehow identical in most of the 6061 tempers, contrasting slightly.
Mechanical Properties
The alloy has three stand out mechanical properties. These include a tensile strength of 260MPa, proof stress of 240MPa and hardness under the Brinell scale of 95HB. The alloy can be solution heated and aged to form the T6 temper which has amazingly superior properties. It’s also important to note that the alloy is supplied in extrusion form.
Other notable properties of this alloy include young’s modulus of 68.9 GPa and Poisson’s ratio of 0.33. The ultimate tensile strength is 310 MPa and has an elongation at break of 17% as well as a fracture toughness of 29MPa/m. The fatigue strength is 96.5 MPa and shear strength 207 MPa.
Heat Treatment
The alloy is prepared through heat treatment at 533 degrees Celsius under which enough time is allowed to give the alloy enough time to form. Then, the product us quenched in water to facilitate completion. After quenching, precipitation hardening at 160 degrees Celsius for about 18 hours follows through. Once this is done, air cooling happens next. The process is repeated at 177 degrees Celsius to complete the development.
Forging happens at temperatures between 233 and 483 degrees Celsius. Other processes done to increase the alloy’s effectiveness are hot and cold working. Where the alloy is worked on in hot and cold water. The range for hot working ranges between 260 and 372 degrees Celsius. For cold working, the temperatures are maintained at 0. These tempering conditions aid the formation of the T4 and T6 tempers. Finally, the 6061 alloys has an annealing temperature of 260 degrees Celsius.
Applications of Aluminum Alloy 6061
This is one of those alloys with the best workability properties in the list Aluminum alloys. For that among other properties, the alloy is another preferred series. Here are some of the applications of this alloy. They include making of the following products:
- Heavy duty structures
- Rail coaches
- Pipelines
- Furniture
- Boiler making
- Ship building
- Truck frames
- Pylons and towers
- Tubes
- Military bridges
There are more applications to this alloy. They include development of essential products in the aerospace and marine industries as well as transport industries. These are areas that require durability due to the continuous provision of services to users.
For instance, Rail coaches travel daily and that means its more likely to wear and tear. Besides, it’s exposes to pressure and hard working conditions like continuous heat and friction. If made out of simple material, it’s likely the coaches won’t operate for long.

Different in Alloy composition
6061 Alloy Composition | 7075 Alloy Composition |
Aluminum – 96.5 | Aluminum – 89.5 |
Manganese – 0.15 | Manganese – 0.04 |
Iron – 0.7 | Iron – 0.3 |
Magnesium – 1.2 | Magnesium – 2.5 |
Silicon – 0.4 | Silicon – 0.08 |
Copper – 0.15 | Copper – 1.5 |
Zinc – 0.25 | Zinc – 5.6 |
Titanium – 0.15 | Titanium- 0.2 |
Chromium- 0.35 | Chromium- 0.28 |
Others – 0.15 |
|
Conclusion
Alloy composition dictates the alloy’s ability to form better performing tempers. It’s important to note that most tempers exhibit better properties than the parent alloy though not all the time. It is for these reasons that tempering is done sometimes to improve the functionality of alloy made products. Alloys 6061 and 7075 have almost similar composition with slight differences in Aluminum, Zinc and Magnesium compositions. This explains the alloys differences in fundamental properties but similarity in applications. Heat treatment has been used to enhance both alloy’s effectiveness in their applications.